Hybrid stepper motors are increasingly vital in today’s automation and robotics landscape, offering precision and reliability for various applications such as 3D printing, CNC machining, and robotics. This article delves into the design features, control strategies, and integration practices of hybrid stepper motors, providing a comprehensive resource for engineers and developers.
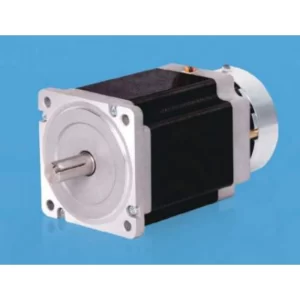
What Are Hybrid Stepper Motors?
Hybrid stepper motors combine the best attributes of permanent magnet (PM) and variable reluctance (VR) stepper motors. They consist of a stator with multiple coils and a rotor featuring a permanent magnet. This design allows high-quality محركات السائر الهجينة to achieve high torque, excellent precision, and reliable performance, making them suitable for applications that require accurate motion control.
Key Design Features
- Stator and Rotor Configuration
- The stator is composed of several electromagnetic coils arranged in a specific pattern. When energized sequentially, these coils create a rotating magnetic field that interacts with the rotor, producing motion.
- The rotor’s permanent magnet enhances the torque output and allows for smoother operation.
2. Step Angle
- The step angle defines the resolution of the motor’s movement. Common step angles for hybrid stepper motors are 1.8 degrees (200 steps per revolution) and 0.9 degrees (400 steps per revolution). Smaller step angles allow for finer control, making them ideal for high-precision tasks.
3. Bipolar vs. Unipolar Motors
- Hybrid stepper motors can be categorized into bipolar and unipolar types. Bipolar motors utilize two coils and deliver higher torque, while unipolar motors have one coil per phase, simplifying control. The selection between these types depends on the specific needs of the application.
Advantages of Hybrid Stepper Motors
- High Precision: They can move in discrete steps, providing exceptional positioning accuracy.
- High Torque: Capable of handling substantial loads without sacrificing speed or efficiency.
- Cost-Effectiveness: Although the initial investment may be higher, their durability and energy efficiency lead to reduced long-term operating costs.
- Ease of Control: Control systems for hybrid stepper motors are relatively straightforward, facilitating easier integration into various applications.
Control Strategies for Hybrid Stepper Motors
Effective control is essential for maximizing the performance of hybrid stepper motors. Here are the primary control strategies:
1. Open-Loop Control
In an open-loop system, the motor is commanded to move a specified number of steps without feedback. This method is simple and cost-effective but may lead to missed steps or inaccuracies, especially under varying loads. Open-loop control is suitable for applications where precision is less critical.
2. Closed-Loop Control
Closed-loop control systems use feedback mechanisms to monitor the motor’s position and adjust commands accordingly. This approach enhances reliability and precision, making it ideal for applications requiring accurate positioning, such as CNC machines and robotics.
Components of Closed-Loop Control:
- Encoders: These devices provide real-time feedback on the motor’s position and speed, allowing for dynamic adjustments to the control signals.
- Controllers: Advanced microcontrollers or digital signal processors (DSPs) interpret feedback data and optimize motor performance.
3. Microstepping
Microstepping is a control technique that divides each full step into smaller increments, allowing the motor to move in finer steps than its standard step angle. This technique results in smoother motion and increased precision, making it particularly useful in applications like 3D printing and precision robotics.
4. PID Control
Proportional-integral-derivative (PID) control is a widely used method in closed-loop systems. By continuously calculating an error value (the difference between a desired setpoint and the actual position), PID controllers adjust the motor's input to minimize this error over time. This method ensures stable and smooth operation, particularly in applications with varying loads.
Best Practices for Integrating Hybrid Stepper Motors
1.Select the Right Motor Specifications
Assess the application’s torque, step angle, and size requirements to ensure the motor meets performance needs.
2. Incorporate Cooling Solutions
Hybrid stepper motors can generate heat during operation, especially under load. Using cooling solutions like heat sinks or fans can enhance durability and maintain optimal performance.
3. Utilize High-Quality Drivers
Invest in quality motor drivers that support advanced control techniques such as micro-stepping and closed-loop control to improve motor responsiveness and performance.
4. Calibrate Your Control System
Regular calibration of the control system ensures accuracy. Adjusting PID parameters or tuning feedback loops can enhance system performance.
5. Conduct Thorough Testing
Before full-scale implementation, conduct rigorous testing and validation of the motor setup to identify potential issues and ensure reliability in real-world applications.
خاتمة
The design and control of hybrid stepper motors are crucial for achieving precise motion control across various applications. By understanding the key design features, control strategies, and best practices, engineers and developers can effectively integrate these powerful motors into their projects. Whether in robotics, CNC machining, or 3D printing, hybrid stepper motors are essential tools for driving innovation and enhancing performance in modern technology. By leveraging their capabilities, you can ensure your projects meet the demands of today’s fast-paced industrial environment.
If you want to buy hybrid stepper motors, you might as well try com.linkmachinery. كمحترف hybrid stepper motors manufacturer, linkmachinery can provide you with high-quality products and services. Welcome to contact us for detailed ordering information and services!